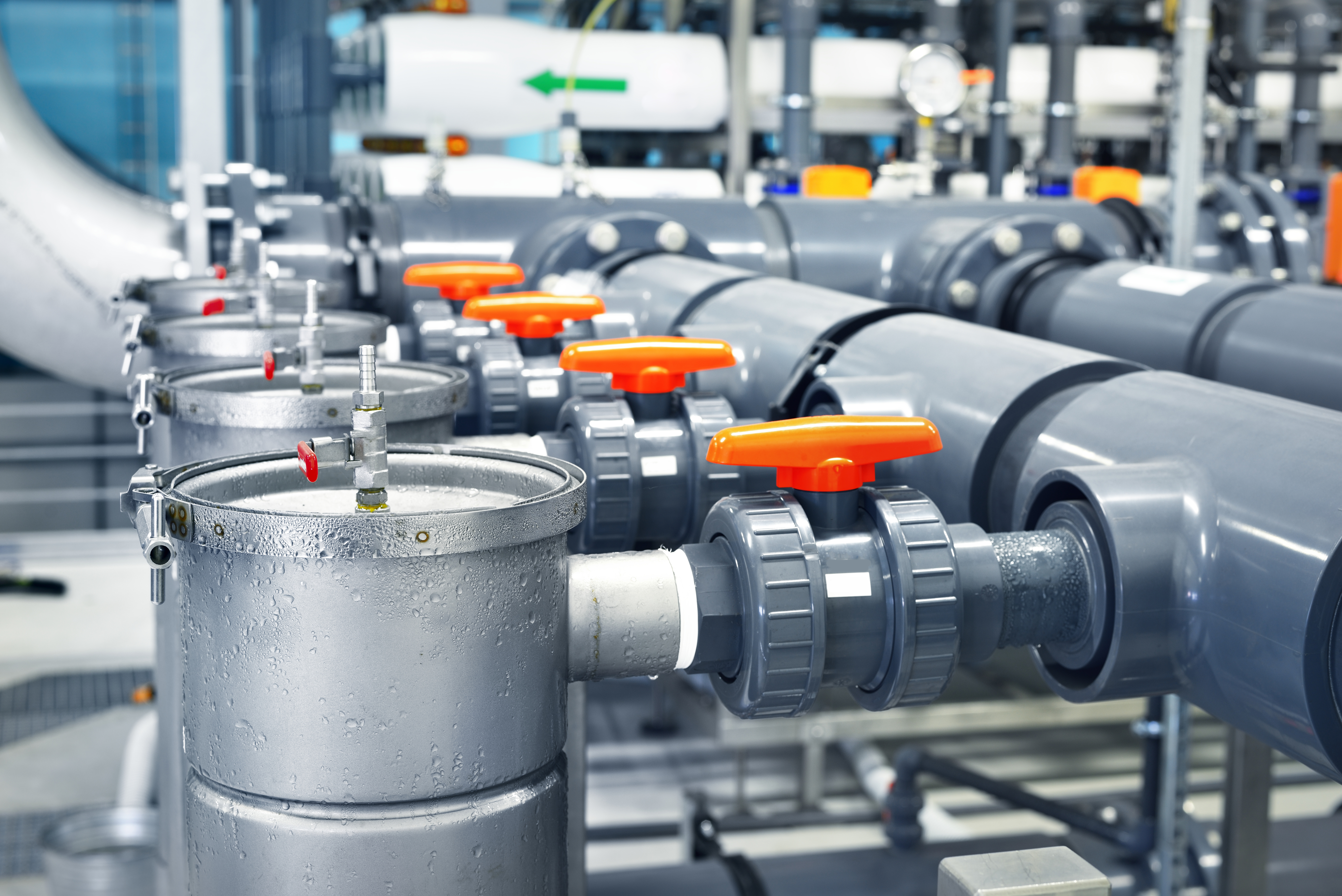
Zero leakage in valves is a highly sought-after characteristic in the industrial and process control industries. The ability to completely prevent any media from escaping through a valve is often necessary to increase efficiency, reduce maintenance costs, and improve safety in operations. But is it even possible to achieve zero leakage in valves?
The answer to this question is not a simple yes or no. The concept of zero leakage is a relative one, and the acceptable level of leakage can vary depending on the specific application and the industry standards that apply to it such as e.g. API598, ISO5208, API6D or FCI 70-2. These standards define leakage rates under specific test conditions and a certain testing time. Especially for soft seated valves these tests call for “0 bubbles of air or 0 drops of water” during the test set-up. Valves tested under these standards are therefore sometimes called “zero leakage” valves. In practice, there is hardly any zero leakage, not even in new valves, since microscopic amounts of material may indeed cross the seat of a valve.
Some examples: Looking at acceptable seat leaking rates for metal-seated valves:
The API598 standard defines the following acceptable leak rates for liquids and gas depending on the valve size:
-
Liquid leak rates range from 5 drops/min up to 96 drops/min
-
Gas leakage rates range from 10 bub/min up to 192bub/min.
However, these leak rates need to be achieved during factory acceptance tests, usually done at the valve manufacturer’s location.
Quality control of valves at the test bench
Once valves are applied in the field, different experiences have been made. Studies show that only after a couple of operating cycles, leakages in valves have already been identified, threatening the smooth operation of industrial processes.
Leaking valves identified after a couple of operating cycles
Depending on the choice of the valve, the user must be aware, that factory acceptance testing with “clean” medium is one thing, applying the valve on site where you might have e.g. particles of sand in natural gas, can be completely different.
In addition, many companies currently do not test valves for leakages once applied on site, which often leaves them undetected until they cause operating problems.
Regular inspection of valves during the operation with technologies such as acoustic emission is therefore highly recommended and can support companies in identify leaking valves long before they can cause any damage to the equipment or pose a danger to employees.
Valve inspection with acoustic emission
Conclusion:
Zero leakage in valves is theoretically possible in post-production quality control, but standards already specify a small acceptable leakage, depending on the valve type and size. After installation on site, however, operators are often faced with other challenges. Modern technologies such as acoustic emission can support companies in valve inspection during the running process and detect even small leaks in time.
Leave Your Comment Here