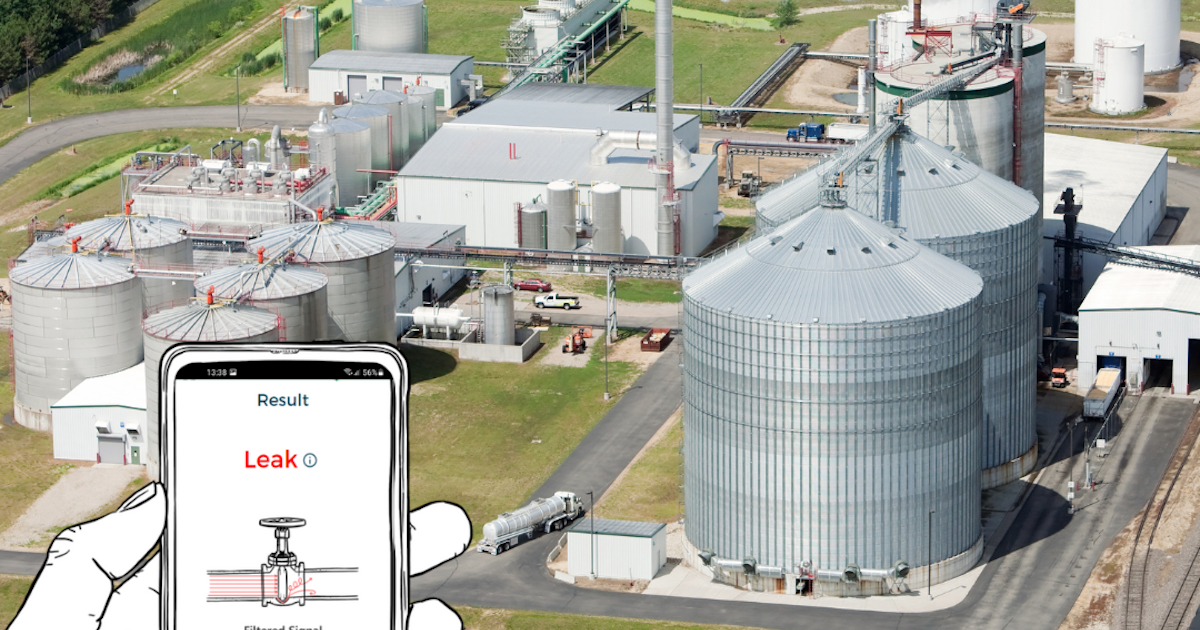
Senseven supported an ethanol production plant in identifying leaking valves and avoiding high economic impacts
Ethanol is known as a first generation biofuel. It is produced commercially in ethanol production plants, also considered as biorefineries. The main basic steps of ethanol production are:
1) Fermentation
2) Distillation
3) Dehydration
Dehydration is the most important step in order to produce high quality fuel. Conventional ethanol distillation can only attain a purity of 95.5% ethanol, with the residual 4.5% being water. Quality fuel, however, requires a dehydrated ethanol to nearly 99.9%. In order to remove the remaining water, other techniques are required, most commonly extractive distillation with molecular sieve. This process is complex and energy intensive and leaking valves in these critical areas are a main challenge for companies and can make it difficult to meet product purification and emission requirements.
The situation today however shows, that there is still a lot of potential here
-
Switching valves in these processes are hardly inspected, rather routinely replaced during scheduled maintenance shutdowns.
-
Companies do not have the required know-how to inspect valves.
-
As a consequence, there is a great risk of reducing the performance of a molecular sieve unit, wasting energy and risking product quality.
Leaking valves on a molecular sieve system can have multiple costs/implications for the plant
-
The vacuum heat used for the regeneration of sieve beds is less efficient and it takes more time if valves are not tight.
-
More steam needs to be generated to compensate the leaking heat capacity.
-
Plant capacity is reduced by up to 5%.
-
Lifetime of sieve beds is reduced – replacement means an investment in the 7-digit range.
On-site inspection supported by Senseven
Facts:
-
Plant capacity of 100 million gallons per year
-
Ethanol price: ~ USD 0,75/gallon (average price assumption)
-
Inspection service provider tests sieve valves using Senseven’s inspection system
Results and implications
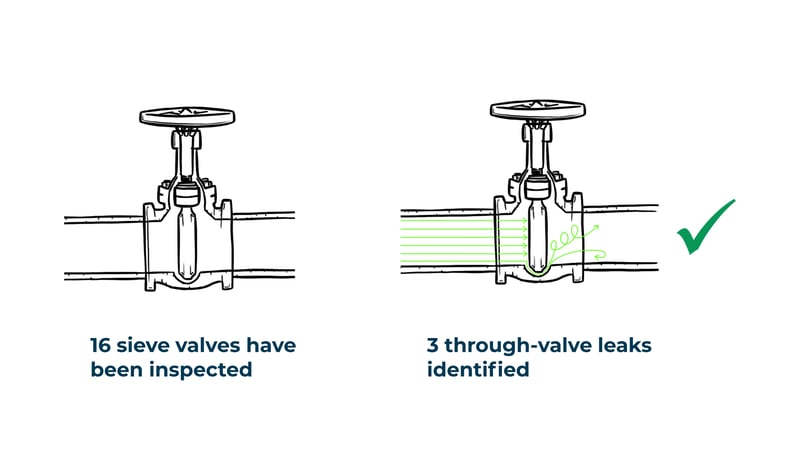
-
These leaking valves have a negative impact on dryer efficiency, causing energy (steam) loss
-
They are negatively impacting the performance of the molecular sieve unit, risking product quality
-
The leaking valves might get the company in trouble complying with increasingly strict fugitive emission requirements
-
These valves can cause a capacity reduction by up to 5%
- Without taking action, the economic impact of product loss amounts up to > USD 3.5 mn/year
"Valve Sense provides a great opportunity for companies with little know-how in valve inspection. It is easy to use, inspections can be performed anytime, and companies can rely on the performance of their valves without having to wait for the next maintenance cycle”, said Shawn Anderson | Chief Engineer at API Solutions.
Leave Your Comment Here