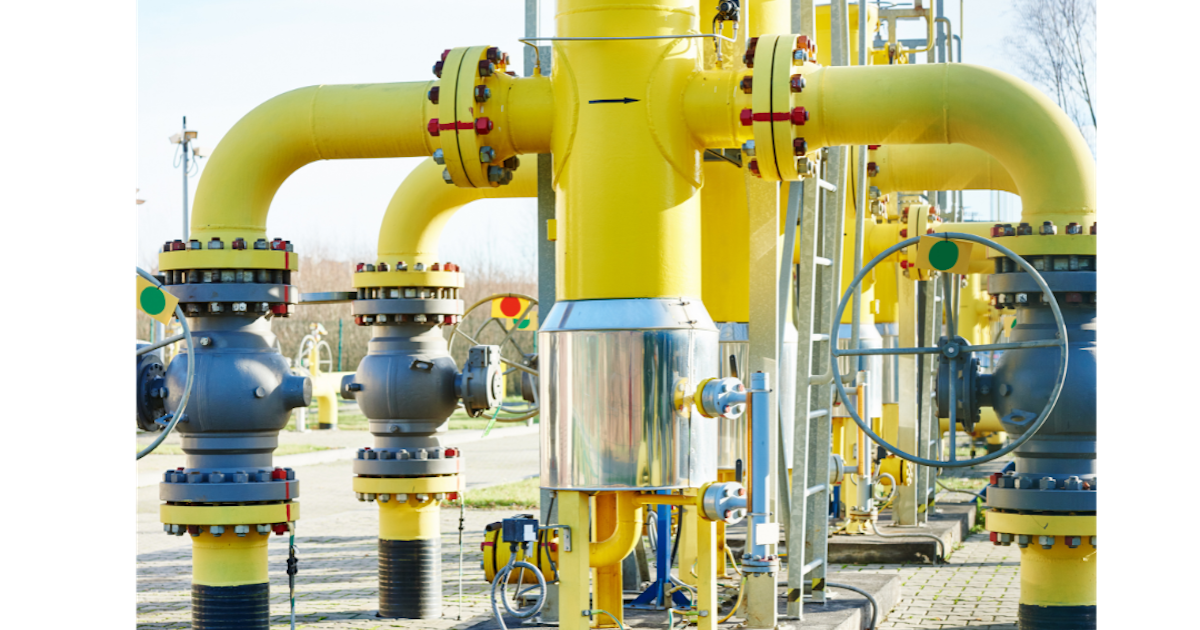
A valve is a device used to control fluid flow through a pipe or duct. The valves control flow for example when starting flow, preventing backflow, and controlling and relieving pressure. Valves are of various types, and their applications depend on the purpose they should fulfill, but they all help to ensure industrial processes' smooth and safe operation. Intact valves safeguard media quality and safety for employees as any fluid leakage, primarily flammable and corrosive fluids, can be hazardous. Also, such leakages may lead to damages of equipment, contamination and, thus, loss of money. A valve requires proper inspection and preventive maintenance to guarantee its functionality. One of the easiest and well-established ways to check for inner valve leakage is using the acoustic emission technology.
Acoustic emission testing for inner leak detection in valves
An acoustic emission test for leakage is a non-destructive test method used to determine if there is inner leakage in valves during operation. One advantage of this technology is that leak detection is performed without disassembling the valves. A leakage in the valve leads to high-frequency stress waves created by turbulence due to the flow that occurs when a medium flows through the leak hole of the valve. Through regular inspection, signal changes are detected early enough, and internal leakages are found before they can cause a major damage to the equipment or harm employees.
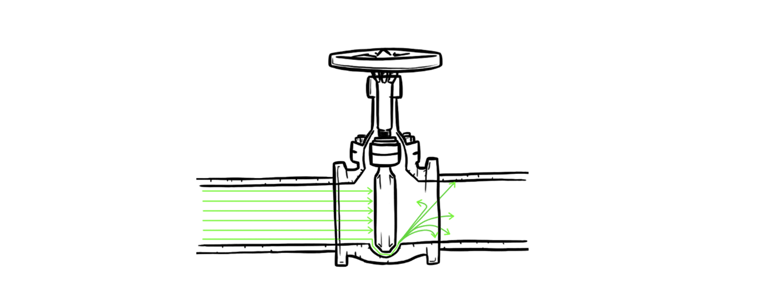
Figure 1: Turbulence created by inner leakage
In valves, any fluid/gas leakage is turbulent. As such, this turbulence generates a fluctuating pressure field that leads to a rise in acoustic emission signal. AE signal is transmitted via the valve wall and the media, making it detectable on the valves outside. At the time of the test, the valve is closed with a specific pressure difference (minimum 1 bar) applied across the valve. A sensor is in contact with the valve surface. The measurement is performed on various points on the valve (see Figure 2), after which the highest stable value is recorded. AE technology can even be used in noisy environments, such as adjacent to pumps and compressors.
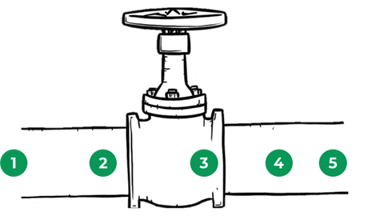
Figure 2: AE measurements performed on 5 points along the valve body
So, for which valves does AE testing work?
Gate valves, Plug valves, Ball valves
Gate, plug, butterfly, non-return (check valves) and ball valves are type of valves that close or open fluid flow. They operate by moving a gate/plug-shaped disk or ball-shaped disk upwards or downwards, normal to the fluid flow, to either open or close. They are used in various applications such as water supply, chemical processing, mining applications, paper, and pulp industries, oil refineries, and steam power plants, among others. These valves are mostly made of steel or iron. The use of steel/iron is meant to add high strength to the valve, suitable for high-pressure and high temperature applications and abrasive materials.
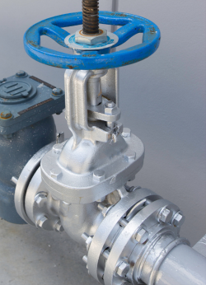
Figure 3: Gate valve as example for on/off valves
Control valves
Control valves are meant to regulate the flow of fluid through a pipeline. Control valves operate by tilting the control disk relative to the direction of fluid flow. There are various control valves: globe valves, butterfly valves and pinch valves, among others. Each type of control valve may operate slightly differently relative to the others. They are very strong due to the high-strength metallic materials used to make them, such as bronze, brass, and stainless steel. Even if these valves are different, they have one common purpose: to protect equipment by regulating flow variables: pressure, amount of fluid, and temperature.
The choice of the valve for a particular industrial process depends on certain factors, which are: the type of media, the valve function, and application conditions. Acoustic emission can be used to identify inner leakage in all the valve types mentioned, irrespective of their size and materials used to make them (brass, stainless steel, zinc, carbon steel, etc.). However, stainless steel conducts signals better among the materials used which could lead to better measurement results, meaning the smallest detectable leak rate might be smaller than for other materials. Also, experience has shown that acoustic emission testing can be difficult on grey cast iron valves because of the graphite which reflects the sound signals.
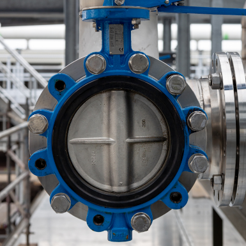
Figure 4: Butterfly valve as an example for control valves
Factors to consider when inspecting valves using acoustic emission
-
Ensure the valve is accessible; that is, it is not covered, for example, by insulation. (Remove insulation or use inspection holes)
-
The temperature on the valve body should not be too high to place the sensor directly on it. The maximum temperature is 150°C; otherwise, use a waveguide.
-
The minimum differential pressure is 1 bar.
-
In large-sized valves, repeat the measurements on the body to enhance accuracy.
Conclusion
Valves are components used to regulate, stop and allow fluid flow in various industrial processes. There are various types of valves, and their applications depend on the plant setup. The two main functionalities of valves are: on/off or control valves. The difference between the two types is that control valves are meant to control flow variables, that is, pressure, flow rate, and direction, and they are more complex. On the other hand, on/off valves are of a simpler design (e.g. gate valves), and they are used for fluid flow shutoff. Fluid leakage in valves can cause injury to the valve operator and lead to environmental pollution and, thus, legal action. One of the ways to check if a valve is leaking is by the acoustic emission technique. Acoustic emission is an already established technology and delivers fast, cost-effective and reliable results. This technology applies to all types of valves irrespective of common construction materials.
Leave Your Comment Here