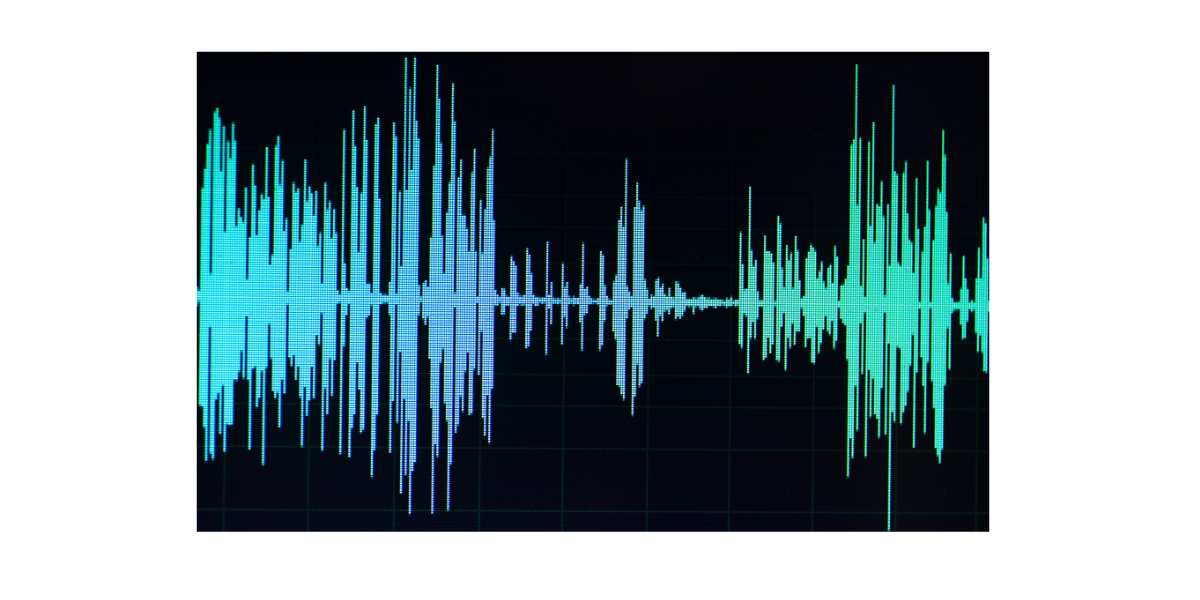
When Max opens the doors to the production halls, he is in his element. While others would hear the drumming, rattling, shaking, and hammering of machines, Max hears the typical operating sound of different machinery components. These machines are a part of his daily work; he is in charge of inspection and maintenance, which is critical to ensuring smooth operation and a safe working environment for his employees.
When it comes to his maintenance activities, sound is an important indicator of the health status of his equipment. Two types of sound commonly used for this purpose are structure-borne and airborne sound. While both methods involve analysing sound, they differ in how they capture and process sound waves, as well as the types of issues they are best suited to identify. Let’s have a look at the key differences:
Air-borne sound/Acoustic condition monitoring
Acoustic condition monitoring is a method to monitor the health status of machinery and components by analysing the sound they produce. So called Air-borne sound is a type of “noise” that is emitted by machines or other equipment in industrial plants and transmitted by air and atmosphere. The sound waves are measured via microphones or other sound sensors in the high-frequency range (20-100kHz) which are typically placed close to the machine. One of the biggest advantages of this method is, that no physical contact is required between sensor and the material under test. The sound data is analysed to detect any changes or abnormalities that would indicate a defect or malfunction. Acoustic condition monitoring is widely used in different industries to inspect rotating machinery, such as pumps, motors and turbines.
Structure-borne sound (acoustic emission as an example)
Structure-borne sound on the other hand is a method to monitor the health status of machinery and components by analysing sound/pressure waves that travel via rigid structures, rather than through the air. They are measured through sensors which are put on the material under test. These sound waves can be produced by a variety of sources, including electrical equipment and mechanical equipment such as motors, pumps and engines under stress. The data collected is analysed to detect any changes or abnormalities that would indicate a defect or malfunction. Structure-borne sound analysis in the ultrasonic spectrum identifies waves with frequency bands of 20 kHz- 1 MHZ.
Which type of sound is better for maintenance activities?
Which method is more useful depends very much on the application and type of defect that is being looked for. The following graph gives an overview how Max is using the different sound phenomena for his maintenance activities:
Airborne sound |
Structure-borne sound |
Electrical inspection:e.g. transformers, generators, |
Electrical inspection:e.g. transformers, generators, |
Wind turbine monitoringe.g. rotating blades |
Concrete testing:e.g. bridges, buildings |
Outer leak detection:e.g. in pipes, tanks, vessels |
Inner leak detection:e.g. in valves, steam traps |
Building inspections:e.g. noise through walls, floors, ceilings |
Bearing inspection:e.g. Bearing failure |
Conclusion:
Structure borne sound and air-borne sound are both important tools for maintenance personnel like Max. Each type of sound has its own strengths and weaknesses, and the choice between them will depend on the specific needs of the maintenance activity. By understanding the differences between the two, maintenance personnel can choose the best tool for the job and ensure that equipment and machinery are operating at their best. And one last important note to end on: Both types should not be confused with the active ultrasound method, but more on that soon in another article.
If you want to learn more about Senseven’s inspection system for structure-borne sound (using acoustic emission technology), get in touch: office@senseven.ai
Leave Your Comment Here