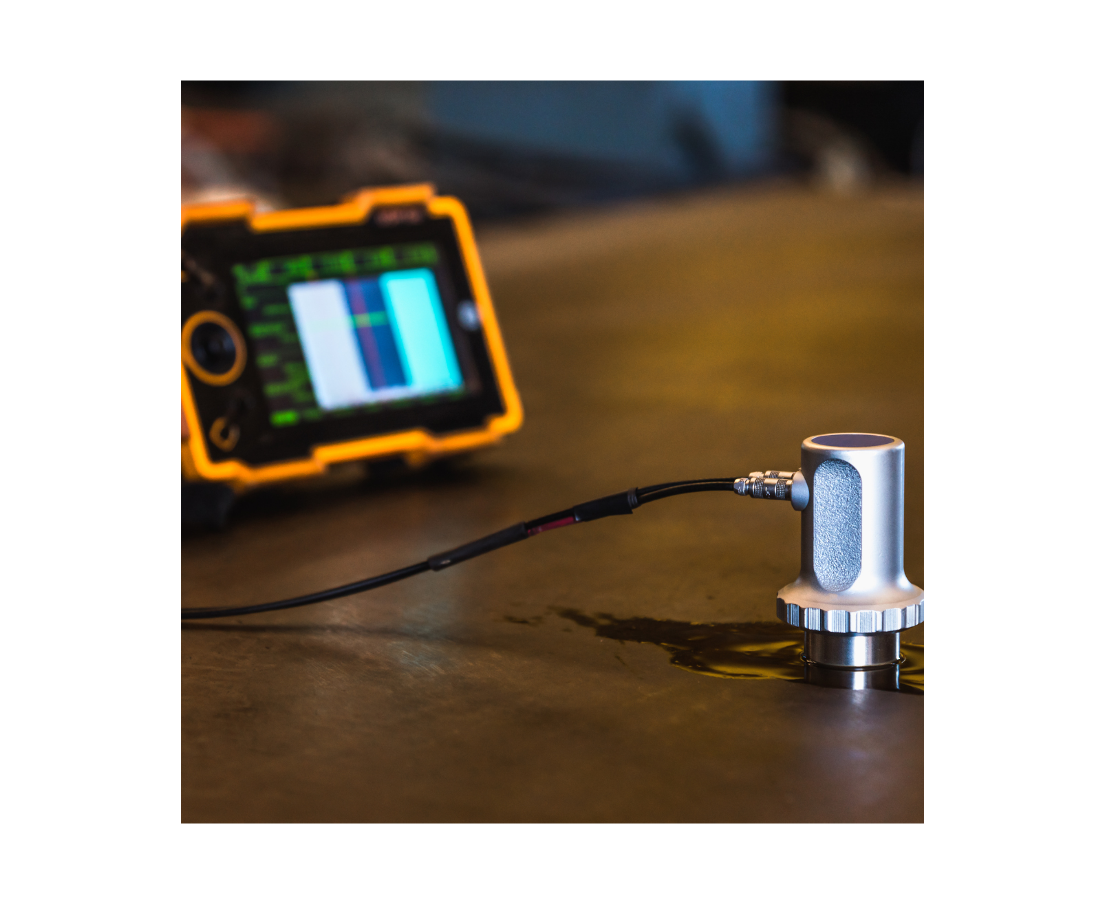
Max, our head of inspection and maintenance in a plant, is using different NDT methods for evaluating the properties of a material or component. Among these methods he uses active ultrasound (ultrasonic testing) and acoustic emission testing (AET) for detecting flaws and monitoring structural health. In this article, we will provide a simplified overview of these two techniques and present a comparative analysis of their key characteristics, differences and applications.
Let’s have a look.
Understanding Active ultrasound (ultrasonic testing):
Active ultrasound (often also called ultrasonic testing) uses an external energy source, typically generated by a piezoelectric transducer, to produce high-frequency ultrasonic waves. These ultrasonic waves are pulsed into the material with different possibilities to analyze signals.
Through-transmission:
Two transducers are placed each on the opposite sides of the material being tested. One creates the pulse, the other receives it. If there is a disruption, inspectors know a defect is present in the path.
Pulse echo:
The same transducer is pulsing and receiving. It analyses echo/reflections received by the transducer. Knowing the velocity at which sound travels through the part, along with the time of travel, provides valuable information for maintenance personnel and allows to detect and report flaws in the material that can lead to asset failure.
Active ultrasound is commonly used, but not limited, to measure material thickness, but also to detect cracks, voids and delamination. By using ultrasonic testing, inspectors are looking for defects which already exist.
Understanding acoustic emissions:
Acoustic emission testing in contrast, is a passive testing method. Instead of supplying energy to the object under examination, acoustic emission testing “listens” for the energy released by the object itself. When a material is subject to mechanical load or stress, it releases energy. This energy travels in the form of high frequency stress waves.
The waves propagate through the solid to the surface, where it is recorded by a sensor. Also here, the sensor is typically a piezoelectric transducer that converts the mechanical wave into an electrical signal.
The acoustic emission signals can provide valuable insights into the onset, propagation, and location of discontinuity within a structure. Acoustic emission is commonly used, but not limited, for monitoring structural health in industries such as oil and gas, civil engineering and power generation, detecting flaws, testing for leaks and monitoring weld quality.
The table below summarizes the main differences between active ultrasound and acoustic emission:
Characteristic |
Active Ultrasound |
Acoustic emission |
Energy source |
External energy (e.g. piezoelectric transducer) |
Energy released by the material under stress or by a leak flow as a result of pressure difference |
Measurement approach |
Analysis of reflections/transmissions from sound waves |
Detection and analysis of high-frequency stress waves emitted by the material |
Application areas |
Used to measure thickness in material, identify cracks and malfunctioning in materials. It can detect surface and subsurface defects. UT looks for defects which are already there. |
Structural health monitoring, oil and gas, power generation. Ideal for identifying and localizing cracks, leakage, corrosion and faults. It can provide information of the origin and significance of discontinuities in a material. AET is able to identify the initiation and propagation of a flaw. |
So what kind of faults/defects can be identified using the different methods? Let’s have a look at some examples from valve inspection (list is not complete):
Fault/Defect |
Active Ultrasound |
Acoustic emission testing |
Cracks |
✔︎Ultrasonic Testing is a suitable method to detect internal cracks once they occured, as they lead to additional reflection of the ultrasound.
|
✔︎AE can detect internal cracks in valves by capturing the high-frequency stress waves generated during crack formation and propagation |
Internal Erosion |
✔︎Ultrasonic Testing can detect erosion by analyzing changes in ultrasound reflections caused by uneven surface profiles resulting from erosion. It can provide measurements of the remaining material thickness and identify erosion patterns. |
✔︎Acoustic Emission can detect internal erosion in valves by capturing the stress waves generated as a result of particle impacts on the internal surfaces, indicating erosion damage. It can monitor erosion progression and assess its severity. |
Internal leakage |
xNot commonly applied for detecting internal leaks in valves |
✔︎Acoustic Emission can detect leaks in valves by capturing the acoustic waves generated by leak flows as a result of pressure differences. It can identify the presence and location of leaks, even in complex valve systems.
|
Thickness Measurement |
✔︎Ultrasonic Testing excels at measuring material thickness by analyzing the time-of-flight of ultrasound waves, providing accurate thickness readings for valve components |
xAcoustic emission is not suitable for direct thickness measurements as it primarily focuses on capturing stress waves related to the dynamic behaviour of the material. |
Microcracks and micro-structural changes |
xMicrocracks are not detectable as they might not (yet) lead to additional reflection of the ultrasound. |
✔︎AE can detect microcracks and micro-structural changes in valves by capturing high-frequency stress waves generated during crack initiation and propagation at a microscopic level. It can identify early-stage damage that may not be visible or accessible for detection using UT. |
Conclusion:
As we have shown above, although both methods use ultrasound/waves in the ultrasonic spectrum, they are distinct inspection methods.
Both are valuable NDT techniques used in various industries to evaluate the condition of materials and structures. While active ultrasound relies on externally generated sound waves for analysis, acoustic emission focuses on capturing stress waves emitted by the material itself. Understanding the characteristics and applications of these methods helps professionals choose the most suitable approach for their specific NDT requirements, ensuring efficient and accurate assessment of structural integrity.
For leak detection in valves, Max is using Senseven’s smart and mobile inspection system based on acoustic emission. The system helps him to easily collect, interpret and store his acoustic emission measurements and supports him in detecting leaking valves before they can cause any damage to his plant.
Get in touch if you would like to learn more: office@senseven.ai
Leave Your Comment Here