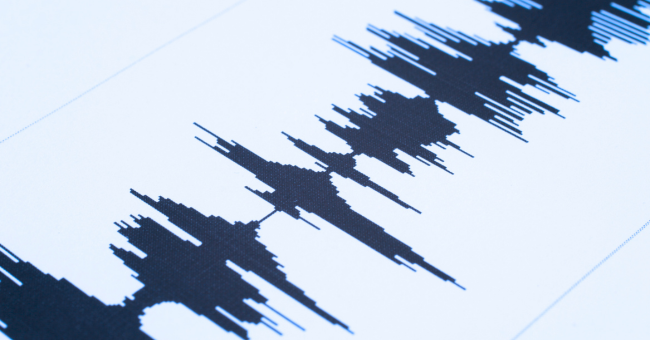
A crucial aspect for Max, head of inspection and maintenance in a plant, is the application of different tools for his maintenance work in order to prevent unexpected failures and ensure smooth operation. You might know Max already from a previous article where we discussed the difference of structure borne vs airborne sound: Read more here.
Other commonly used techniques for his condition monitoring and predictive maintenance are Vibration Analysis (VA) and Acoustic Emission Testing (AET). Comparing these two methods is not always easy. In fact, AE is sometimes colloquially described as the new generation of vibration techniques. - See an article in reliable plant: here as an example.
However, we dare to try to compare the two methods here.
Both methods use sensors in order to detect and analyse signals emitted by machines which are then processing waveforms in the time and frequency domain. The methods might therefore seem similar at first glance and partly overlap in applications, however, there are a few key differences to note. Let’s have a look.
Vibration analysis:
Vibration Analysis (VA) is a method of measuring the movement (vibration levels and frequencies) of machinery and then using the signal information to analyse the health status of machinery components. Anytime a machinery is running, it is making vibrations (both, in a healthy and unhealthy state). Vibration is therefore always present in operational rotating machinery and moving structures. We could also say, it is essentially the monitoring and interpretation of the heartbeat of a specific equipment. To conduct the analysis, sensors are installed on the equipment to record vibrations, which are then analysed to detect any abnormal patterns or frequencies. Defects/Faults must have already occurred to detect a changing signal.
Vibration analysis is commonly used, but not limited, to detect early signs of wear and tear, misalignment, imbalance, mechanical looseness, and other issues on rotating machinery, such as motors, pumps, industrial fan blades, gearboxes etc.
Illustrative: Vibration sensor used for vibration analysis on a pump
Acoustic emission:
By contrast, Acoustic Emission Testing (AET), which also is a non-destructive test technique, detects high-frequency stress waves emitted by changes in materials or structures under load. These waves can additionally also be detected on structures or components where a leak flow as a result of pressure differences appears and generates acoustic emission.
A healthy machinery (in an isolated environment) would therefore not emit any AE signals. In addition, AET is based on higher frequencies compared to vibration analysis. This allows the detection of discontinuity and its progress, even before a defect/fault occurs. AE sensors are typically attached to the surface of the equipment or structure, and the recorded signals are analysed to detect growing cracks, leaks, and other forms of ongoing defects, faults or degradation. AE testing is commonly used, but not limited, for monitoring pressure vessels, pipelines, valves, storage tanks, rotating equipment and other critical assets in industries such as oil and gas, chemicals, pharma, pulp and paper etc.
illustrative: AE sensor used for leak detection in valves
But which method is better suited for inspection and maintenance activities? As with every test method, it depends on the specific application and requirements. Both testing methods have their strengths and limitations and therefore they are often used complementarily. Let’s compare the main characteristics:
Vibration analysis |
Acoustic emission analysis |
Measures mechanical vibrations on the surface of rotating machinery (e.g. motors, pumps, gearboxes,..) |
Measures surface stress waves emitted by smallest changes in the material’s internal structure or waves generated by leak flows as a result of pressure differences (e.g. pumps, valves, pressure vessels,…) |
Frequencies: depending on rotational speed, normally below 20kHz |
Frequencies: ultrasonic spectrum between 20kHz and 1MHz |
Non-intrusive testing: sensors are typically attached to the surface of the equipment without dismantling it, for permanent installation, dismantling of parts could be necessary |
Non-intrusive testing: sensors are typically attached to the surface of the equipment without dismantling it. |
Limited sensitivity to early discontinuity as signals might not change significantly until the defect becomes severe |
High sensitivity to early discontinuity: stress waves are already emitted with smallest forms of discontinuity. It can detect changes in stressed material even before they result in visible signs of defect/fault. |
Can identify equipment wear |
Can identify and localise growing defects/faults |
A lot of research has been done to compare the two methods especially for equipment like bearings as they are considered as crucial components in industrial applications. Some findings listed below:
Vibration analysis for bearing monitoring |
Acoustic emission testing for bearing monitoring |
Probably most established method to monitor bearing degradation |
Mostly used as complementary diagnostic method to vibration analysis for bearing monitoring |
Some degradation/defect must have already taken place to identify abnormal vibration patterns |
Able to monitor bearings before visual defects are formed in contacting surfaces due to high frequency AE signatures |
Able to detect defects in lower frequency ranges, such as imbalance, misalignment and shaft bending |
Unable to detect low frequency defects such as imbalance, misalignment and shaft bending |
It is able to monitor defects in medium to high rotational speeds |
It is able to monitor defects in medium to high rotational speeds, |
Shows its limitations with low-rotation speeds because of the weaker vibration signal produced by lower speed |
Can identify impacts in bearings also in slow-rotation speed |
Sources e.g.
CONDITION MONITORING OF SLOW-SPEED ROLLING ELEMENT BEARINGS USING STRESS WAVES
The use of Acoustic Emission for bearing defect identification and estimation of defect size
ACOUSTIC EMISSION ANALYSIS FOR BEARING CONDITION MONITORING
Combination of vibration analysis and Acoustic Emission measurements to better characterize damage and mechanical behaviour of aerospace high speed rolling bearing
As we have seen above, both methods show their strengths and weaknesses and are therefore often used as complementary diagnostic tools. Both can contribute to Max’s predictive maintenance strategy. Vibration analysis and acoustic emission can be used to identify the beginning of equipment wear (VA) or early stages of defects (AE). That’s the backbone of predictive maintenance.
By continuously monitoring and analysing vibration and acoustic emission data, Max can detect defects in different equipment at an early stage. This offers him numerous benefits such as:
-
Significant reduction in unplanned downtime.
-
Overall improvement of equipment availability and reliability.
-
More control over downtime and maintenance processes as they are less reactive.
-
A reduction in material costs, thanks to less energy losses, less scrap and fewer discards.
-
Reduced maintenance costs.
-
…
For leak detection in valves, Max is using Senseven’s smart and mobile inspection system based on acoustic emission. The system helps him to easily collect, interpret and store his acoustic emission measurements and supports him in detecting leaking valves before they can cause any damage to his plant.
Get in touch if you would like to learn more: office@senseven.ai
Leave Your Comment Here